I am currently traveling for work and since I can't work in my shop I decided to put a little time into planning to makes some needed upgrades to the shop. A few years ago I had built a table for my shop. It was to fulfill multiple jobs and provide some needed storage in the shop. I found and then modified a design from www.thewoodwhisperer.com. Marc Spagnuolo's table design fit almost all of my needs. Well fast forward till now and the table has worked great and really helped in the shop.
One of my design modifications was to put the table on casters. What I didn't do was to add additional support when I put the four casters in corners of the base. Over time due to the extreme weight of the very massive torsion box table top and the lack of structural support in the base it has began to sag in the middle. Right now if you put a straight edge along the length of table there is about a 1/4 inch sag. Now for most of its intended purposes that's not that big of a deal. But using the table as an assembly table it can cause issues for some glue ups. I have also added several other tools like my jointer, planer, miter saw station, and router table to the shop. These additions have taken up a lot of my available floor space I had before. Whats all this mean you ask... well let me tell you. It is time for upgrade!!!
Let me start by saying that once again I'll be taking some design ideas from other sources. This time the top will be from Ron Paulk at www.paulkhomes.com. He created a mobile worktable that is pretty amazing. He is a general contractor and designed it to be mobile. I like how functional the top was. It is constructed similar to a multi-function table by Festool but with the stability of a torsion box top. It has holes drilled in the top to allow clamping and the open side allows for temporary storage of tools you are using and a place to clamp to the side of the table as well. I still want to keep some of the storage of my old table but wanted to shrink its overall footprint. The main priority it still needs to serve is as an out feed table for my table saw, an assembly table, and a workbench. So after a many hours of research and a couple hours of playing around on Sketchup... I present my next workbench plan.
The overall dimensions of the tabletop is 4' X 4". This will give still allow for plenty of work surface while freeing up a little real estate in the shop. I am going to build the entire project from 3/4 inch cabinet grade plywood. Two of the opposing sides are designed the same with a cabinet door and three large drawers which will be mounted on full extension slides. The table will once again be on casters but will be properly supported to hold the weight of the table. I also took the time to do a cut list for the project to minimize waste.
I use a cut list primarily on large projects to help me figure out my lumber needs and also when dealing with sheet goods to help minimize waste. Now all that's left is for me to get home, purchase some lumber, and start making some sawdust.
Sunday, May 18, 2014
Monday, May 12, 2014
The great triple bunk bed build
I just wanted to take a moment to talk about one of my projects this year. I had a client contact me to build a triple bunk bed for his three little girls. He sent me a couple different photos he had found online and we discussed everything from style to method of construction to material used. Each of these thing not just effect the bottom line but also the finished product. So armed with this information I started to draw up some plans. The design the client wanted was found online and has been used by several people. I'm not sure who originally came up with design but my hats off to them. I made some changes so that the bed would fit the girl's bedroom.
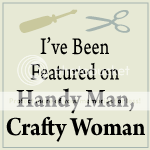
I use google sketch up to draw up my plans. I am still new to the program but there is a plethora of YouTube tutorials available. It really helps to have a scale drawing to help figure out how much material you need to purchase and how everything hopefully will look when I'm finished. Stability and strength were the clients biggest concern and to match the other decor that was going in the room they wanted the bed painted white. To keep the price in their goal range and keep structurally sound we went with dimensional construction grade lumber.
The first step was to build the three identical frames that the mattresses would sit in. I know a lot of beds use slats but as a child that survived a bunk bed collapse because of a sibling jumping on the bed above me I suggested a solid bottom. Now here is where I came upon my first little bump in the road. Since I wasn't installing the bed in my own house and I really couldn't build it in the clients home I had a little bit of a available room issue. Luckily for me I have a completely supportive wife who let me take over the living room for awhile.
From there I was able to start cutting and constructing the vertical supports. I started from the floor and built my way up to the top. This way each piece was cut as needed and I wasn't relying on a cut list or plan. Not there is anything wrong with either of those but in my experience a plan is only as good until the first problem or issue.
In the picture you can see how each bed is not only secured by lag bolts but a physical joint for added strength.
By building from the ground up it allowed me to be one step ahead of adding an additional level with structural support.
Building a triple bunk bed in the middle of your living room sure does make the space seem much smaller. I also made sure that as I built the bed it was designed to be able to be taken apart first so that I could deliver it to the client but then also down the road if he wanted to move he could take the bed with them. But first I had some painting to do.
The living room once again prove very useful in this part of the build. I did a good deal of the painting outside but as it started getting dark we had to move it inside. Once the paint was dry it was time to deliver and set up.
There is every so often a moment when I question my decision to downsize to a smaller truck... but them she pull through for me and we make it happen. This was one of those moments. I recruited the help of one of my friends and we loaded up the bed and headed out to set up the bunk bed for the client.
The client was very pleased with how the bed turned out and so was I. I hope those girls get many years of enjoyment out of this huge structure that they will share nightly as they go through their childhood. I still have many fond memories of playing on our bunk beds as kids with my brothers. Please feel free to contact me if you have any questions with this or any other project. I enjoy building, sharing, teaching, and learning and make time to do all of them. You can read about my other projects HERE or follow me on facebook at www.facebook.com/MerzkeCustomWoodworking. Thanks for stopping by and I look forward to hearing from you.
***********************************UPDATE************************************
You can now purchase the plans and SketchUp file for the Triple Bunk Bed from
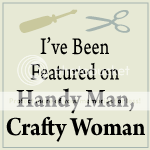
Sunday, May 11, 2014
Found a new home...
Well it wasn't me!!! I don't need a new home. But instead of trashing the old upper kitchen cabinets I've found a new home for them. Also, all my stains, dyes, and finishes in turn found a new home. It just worked out that both could help each other out. A couple coats of paint and a french cleat on the back and we were in business. Kelly had a great idea to try chalkboard paint on the panels of the doors so I could use them as a chalk board. I purchased some chalkboard spray paint and put a couple coats on. After the paint dried I attempted to make a to do list for myself... but to my disappointment it was very hard to write on it.
I think I'm going to pick up some brush on chalkboard paint, lightly sand the surface and try rolling on a final coat and see if that helps. I did however provide more than enough storage for all my finishing products.
Another step down in making the old shop a little more organized. I was also able so save one of the other smaller upper cabinets that I will eventually slap a couple coats of paint on. I did put a french cleat on it and it fit perfectly over my dust collector.
As far as the home improvement projects are coming it can be summed up in one word... SLOW!!! We started putting baseboards and shoe molding in the half bathroom today and got the toilet and sink installed.
The sink went in with no issues. Even with the floor raised a little because of the tile I was still able to use the original holes to secure it to the wall. The toilet on the other hand needed a spacer to make up for the difference of the new flooring. All that and a new toilet seat and we were in action.
Unfortunately the project will have to take a little break because of my upcoming work schedule. But I'll be back at it before you know it.
I think I'm going to pick up some brush on chalkboard paint, lightly sand the surface and try rolling on a final coat and see if that helps. I did however provide more than enough storage for all my finishing products.
Another step down in making the old shop a little more organized. I was also able so save one of the other smaller upper cabinets that I will eventually slap a couple coats of paint on. I did put a french cleat on it and it fit perfectly over my dust collector.
As far as the home improvement projects are coming it can be summed up in one word... SLOW!!! We started putting baseboards and shoe molding in the half bathroom today and got the toilet and sink installed.
The sink went in with no issues. Even with the floor raised a little because of the tile I was still able to use the original holes to secure it to the wall. The toilet on the other hand needed a spacer to make up for the difference of the new flooring. All that and a new toilet seat and we were in action.
Unfortunately the project will have to take a little break because of my upcoming work schedule. But I'll be back at it before you know it.
Thursday, May 8, 2014
A trip to the lumber yard!!
So today I was able to sneak out of work and go get the lumber for my countertops. Originally we were going to make the countertops from 8/4 solid walnut. Rough cut lumber thickness is measured in quarter inches. So eight quarter (8/4) is two inches. After doing some research and looking around we decided to go with solid hickory. Not only is it a harder wood than walnut but also cheaper. I was able to borrow a small trailer from a friend of a fellow woodworker who was coming along for the trip. Several other woodworkers I know had recommended Steve Wall Lumber for purchasing the material for the countertops. I can get Red Oak and Poplar from a local Saw Mill here in Raeford but if need anything more "exotic" I'm going for a drive.
Wall Lumber is located about 25 miles north of Greensboro, NC. We hooked up the trailer and off we went. A short two and a half hours later and we pulled into their parking lot. At that point I felt like a kid in the candy store. The clouds parted and angels even began singing. Before me stood a huge warehouse full a kiln dried goodness. The smell of fresh cut lumber permeated the air. From just about ever domestic hardwood to some of the most popular exotics there was lumber for as far as the eye could see. Not only did they have a huge selection of lumber milled from thin stock project packs to huge slabs with live edges. The staff were very friendly and knowledgeable. They also offer milling services, moldings, and a wide assortment of sheet goods. This was a pure field trip for a couple of woodworkers. But business called. I selected a little over 120 board feet of Hickory, some Hard Maple, and a little Sapele. This was my first time buying real "exotic" hardwood. It is marketed as a good alternative for Mahogany. The Hickory is for my countertops and the Maple and Sapele will be for a frame for a couple of American Flags flown over Afghanistan (upcoming project).
After a couple hours of drooling at the thousands of board feet of lumber in stock we loaded up the trailer and strapped it down for the long drive home. We had to drive a little slower on the way home due to the load on the trailer. But finally made it home with the same amount of lumber we left with. With all the home improvement projects ongoing lumber storage is definitely an issue. We did get to put the kitchen back together the other night so...
Now I'm not sure if I've mentioned this lately but I have the most amazing and loving wife EVER. What wife out there openly allows for the storage of over a 120 BF of Hickory on the kitchen table? Mine does!!! I can't wait to mill this lumber down and hope it turns into kitchen countertops. At least the easy part is done. Thanks again to guys at Steve Wall Lumber. I will definitely be back (maybe with a bigger trailer).
Wall Lumber is located about 25 miles north of Greensboro, NC. We hooked up the trailer and off we went. A short two and a half hours later and we pulled into their parking lot. At that point I felt like a kid in the candy store. The clouds parted and angels even began singing. Before me stood a huge warehouse full a kiln dried goodness. The smell of fresh cut lumber permeated the air. From just about ever domestic hardwood to some of the most popular exotics there was lumber for as far as the eye could see. Not only did they have a huge selection of lumber milled from thin stock project packs to huge slabs with live edges. The staff were very friendly and knowledgeable. They also offer milling services, moldings, and a wide assortment of sheet goods. This was a pure field trip for a couple of woodworkers. But business called. I selected a little over 120 board feet of Hickory, some Hard Maple, and a little Sapele. This was my first time buying real "exotic" hardwood. It is marketed as a good alternative for Mahogany. The Hickory is for my countertops and the Maple and Sapele will be for a frame for a couple of American Flags flown over Afghanistan (upcoming project).
After a couple hours of drooling at the thousands of board feet of lumber in stock we loaded up the trailer and strapped it down for the long drive home. We had to drive a little slower on the way home due to the load on the trailer. But finally made it home with the same amount of lumber we left with. With all the home improvement projects ongoing lumber storage is definitely an issue. We did get to put the kitchen back together the other night so...
Now I'm not sure if I've mentioned this lately but I have the most amazing and loving wife EVER. What wife out there openly allows for the storage of over a 120 BF of Hickory on the kitchen table? Mine does!!! I can't wait to mill this lumber down and hope it turns into kitchen countertops. At least the easy part is done. Thanks again to guys at Steve Wall Lumber. I will definitely be back (maybe with a bigger trailer).
Wednesday, May 7, 2014
Just a little update...
So I am happy to say the tiling is finished. I think it came out beautifully if I do say so myself... BUT what an endeavor. Once we had tackled the learning curve things moved pretty quickly. Well, as quickly as two people with full time jobs and one of them traveling for work a lot can do.
The only step to finishing the kitchen floor is baseboards and shoe molding. The half bathroom still needs some touch up paint and then the baseboards and shoe molding. Then we can get the toilet out of our living room and put it back where it belongs. You never realize how nice it is to have a toilet so close until is is out of order and you have to run all the way upstairs to take care of business.
Once the flooring in the living room is finished I can start working on all the small tasks like:
1. Upper kitchen cabinets
2. Kitchen island
3. Wood counter tops
3. Laundry room cabinets and drying rack
4. Mud room cabinets
5. Kitchen table and benches
6. Stools for kitchen island
7. Wanes coating for back-splash
I am sure I'm missing a half dozen to a million other things I need to cross of my list till I can call this project complete. The good news is that as we complete each step along the way you can watch the transformation from blah to BAM!!!
Ok, so that might of been a little over kill but whats a guy to do. Well I am off to work and will keep you posted as the project moves along.
The only step to finishing the kitchen floor is baseboards and shoe molding. The half bathroom still needs some touch up paint and then the baseboards and shoe molding. Then we can get the toilet out of our living room and put it back where it belongs. You never realize how nice it is to have a toilet so close until is is out of order and you have to run all the way upstairs to take care of business.
Once the flooring in the living room is finished I can start working on all the small tasks like:
1. Upper kitchen cabinets
2. Kitchen island
3. Wood counter tops
3. Laundry room cabinets and drying rack
4. Mud room cabinets
5. Kitchen table and benches
6. Stools for kitchen island
7. Wanes coating for back-splash
I am sure I'm missing a half dozen to a million other things I need to cross of my list till I can call this project complete. The good news is that as we complete each step along the way you can watch the transformation from blah to BAM!!!
Ok, so that might of been a little over kill but whats a guy to do. Well I am off to work and will keep you posted as the project moves along.
Subscribe to:
Posts (Atom)